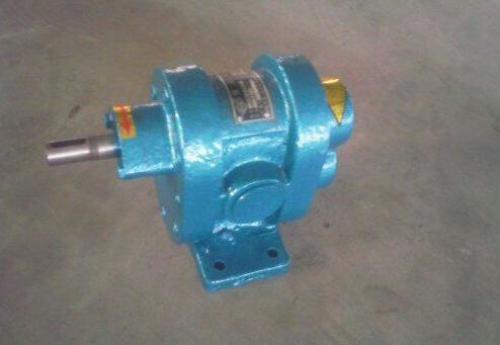
Residual oil pump wear material processing
Residue oil pump is currently used as a wear-resistant part material and high-chromium cast iron is used. It is one of the best domestic wear-resistant materials. Most of the media handled by the slurry pump are high-abrasive slurry with high concentration. Therefore, the slurry pump itself requires high wear resistance and corrosion resistance of the manufacturing materials.
The machining tool of the wear-resistant material of the residue pump has made certain breakthroughs in recent years with the advancement of technology. It is a new ceramic tool in ceramic products. Ceramic cutters are characterized by their high strength, high hardness, good wear resistance, good chemical stability and low friction coefficient. They have great advantages in the field of machining wear-resistant materials like slurry pumps.
Residue pump production companies or supporting parts processing companies, all need to deal with high chromium cast iron and other wear-resistant materials, the general use of machining tools is alloy tools, such processing methods complex process, high cost and low efficiency, can be said that high chromium The difficult machining of cast iron has always been a problem for slurry pump producers.
Slag pump manufacturers and supporting parts processing companies are also gradually promoting and using ceramic tools, according to the use of the situation, ceramic tools can really solve the problem of high-chromium cast iron machining problems. At the same time, the use of ceramic cutting tools can also effectively reduce the production cost of the slurry pump and significantly increase the production efficiency, which can bring higher economic benefits to the company.
Residue pumps are widely used and promoted in different industries, showing good use value in the industry. The residue pump is mainly used for mining, dredging, transportation of tailings, slime, iron powder, etc. in mines, metallurgy, coal, electricity and other engineering projects.
Causes of cavitation in residue pump
The pressure of the residue pump fluid decreases from the inlet of the pump to the inlet of the impeller, and the liquid pressure near the vane is the lowest. The partial pressure of the residual oil pump in operation partially causes the absolute pressure of the pumped liquid to drop to the gasification pressure at the current temperature. The liquid vaporizes at this point, and there may also be gas in the liquid overflowing from the solution. Many bubbles are formed. These bubbles flow forward with the liquid. When the pressure is higher in the leaf, the pressure of the liquid outside the bubble is higher than the pressure inside the bubble. The vaporization pressure of the gas will be reduced sharply and the bubbles will collapse to form cavities. At the same time as the bubbles shrink and break, they will have a large impact pressure, which can reach several hundred atmospheres, form a water hammer, and continuously strike the metal surface. Shock and fatigue peel off. The occurrence of this phenomenon causes the corrosion of the flow-through components, and the above-mentioned process of generating bubbles and bubbles that drastically reduce and even destroy the ruptured flow-through components is the cause of cavitation during the operation of the residue pump.
The pump over-flow part of the residue pump operated under cavitation for a long time will be corroded and destroyed. This is due to the strong impact on the metal surface when the bubbles condense and the metal surface appears pitted. In severe cases, the metal grains are loosened and peeled off. Even in the form of perforations, cavitation is accompanied by the destruction of mechanical forces, as well as a variety of complex forces such as electrolytic chemical corrosion. Practice has shown that radical cavitation must prevent air bubbles in the flow path of the pump during operation.
Nowadays automation equipment is used widely. Automation parts or components play the important role in automation equipment.We can manufacture various high precision automation parts as customers' requirements. We have advanced production and measurement equipments. The torlerance can be 0.001mm. High precision with competitive price. Strict quality control. Short lead time. OEM orders are welcomed. Our main customers come from Europe, American, Japan etc
Injection Molding Parts,Injection Mould,Metal Machine,Customized Automation Parts
KUNSHAN YSL PRECISION MOULD CO.,LTD , http://www.yslprecisonmould.com